Attracted by huge market opportunity in power plants and chemical plants, most manufacturers have made great effort to improve processing technique and reduce cost, which makes insulation aluminum coil win more and more popularity in protecting pipelines. As a matter of fact, compared to traditional metal alloys, aluminum coil, mostly series 5 (for more information, please refer to Aluminum Coil Used For Car Frame) has natural advantages for insulation.
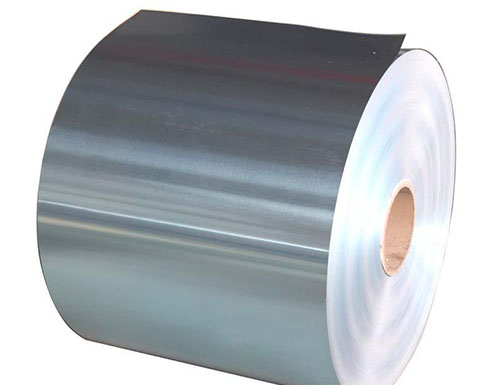
First, it has long service life. Pipelines are usually located in severe environment and exposed to moisture, corrosive bacteria, and sunshine all the year round. Metals like iron and zinc go rusted easily in only several years. In the past pipeline coatings, made of iron and zinc, had to be maintained frequently and replaced every two or three years, causing great waste of human and material resource. Insulation aluminum coil, with perfect weather resistant ability, became an ideal substitute. It almost never rusts, thus there’s no trouble of maintenance and replacement. Second, it’s more attractive by look. Iron and zinc coatings, after being oxidized and rusted, become dark and ugly. In contrast, aluminum coil has a natural bright silver color which, benefiting from the material’s excellent weather resistance, won’t change with the passage of time. Snakes of sliver pipelines can be a proud scene for any plant. Third, it’s recyclable. It’s hard to make good money from rusted iron and zinc materials, but bright used aluminum coil coatings will lose little market value. Plants can sell them and bring back most the cost.