Aluminum sheet refers to a kind of rectangular material that made of pure aluminum or aluminum alloy, with a rectangular cross-section and an uniform thickness. In general, the aluminum material with a thickness of 0.2mm or more, 500mm or less, a width of 200mm or more and a of 16m is called an aluminum plate, and the aluminum foil has a thickness of 0.2mm or less.
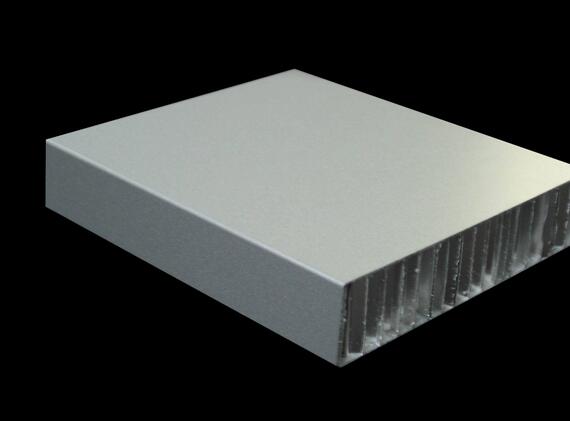
Aluminum sheet is a solid material and an almost entirely pure element. When properly used in architectural applications, it is cut into sheets, fabricated and formed, then post-finished. The exterior side is finished in a spray-applied PVDF coat, normally warranted for 10 or 20 years, in compliance with ASTM D-4214 (chalk resistance). Warranties have been known to altogether omit ASTM D-2244 (fade resistance) or allow application tolerances of ∆2, per D-2244. AAMA 2605-05 even states that “exact color uniformity should not be expected” when using “pearlescent mica or metallic” finishes. Reiterating this point in the interest of clarity, the material is delivered and installed exhibiting ∆2 color differences, and color fade begins afterward, exempt from any warranty obligation. The interior side of aluminum sheet is finished with primer, unless otherwise specified
Aluminium Composite Panels as aluminum panel sheet are available in various widths & thicknesses depending upon the intended application. The range is further expanded into Fire Retardant and Stone Finish panels in attractive colours and patterns
As a new decorative material, aluminum composite panel enjoy high favor among people quickly, because it has a various colors, convenient construction methods and an excellent processing performance. Aluminum composite panel consists of metal and non-metallic, it retain the main features of the original composition of the material (aluminum metal and non-metallic polyethylene plastic), also overcome the shortcomings of the original composition, and get a lot of excellent performance.
Aluminum composite panel and aluminum sheet have some of the same material composition and some common excellent performance, but their application and processing methods are significant different. However, the aluminum composite panel may go wrong after decoration, in a way, aluminum sheet is more sturdy and durable than the aluminum composite panel
aluminum composite material (ACM) is a thermoplastic core, chemically-bonded to two prefinished aluminum sheets, usually 0.02” thick (equivalent to 25-gauge). The exterior sheet is coil-coated with a high-performance PVDF coat, normally warranted for 30 years, in compliance with ASTM D-4214 (chalk resistance) and with ASTM D-2244 (fade resistance). The interior sheet is finished with a siliconized polyester paint in a random color, unless specified otherwise.
ACM does have some inherent disadvantages: sheet widths are limited to 62”; the material cannot be welded without material failure; it is not meant to be used in roll-forming or break-metal applications; and producing small quantities of custom colors can be cost prohibitive. In contrast, the heavier aluminum gauges of aluminum sheet can be welded, and the lighter sheet/coil gauges can be used in roll-forming and break-metal applications. Aluminum sheet also allows for custom color since no post-applied color is significantly more or less expensive than any other color. Aluminum sheet is, however, limited in maximum width and is much more prone to visible oil-canning, despite its increased material cost.