aluminum foil strip and coil in appropriate strip widths and lengths to conduct the electrical currents involved in coil applications, have widely replaced wire in electrical transformers, from large power distribution sizes down to small transformers designed for a variety of uses including welding machines. aluminum foil strips conductor is also employed in a variety of control units, holding coils, electromagnets, and others.
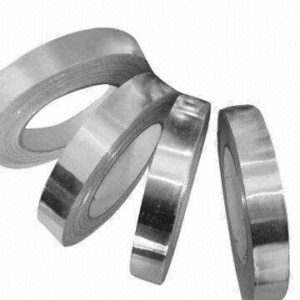
aluminum foil strips for electrical coil application ranges from 0.0006 to 0.0059 in. Several aluminum alloys can be used to meet the minimum industry requirements for strip conductor, but alloy 1350 (99.50% aluminum) is generally the low purity limit employed for this application.
Slitting is closely controlled to assure smooth, substantially burr-free edges and strip-size availabilities are in capacities exactly equivalent to those of standard copper wire sizes.
In varying degrees, for different electrical applications, the following advantages of aluminum foil for aluminum coil winding are typical:
Depending upon the market, significant material savings, as compared with conventional wire windings, are affected through the use of the convolute-wound aluminum coils. In some instances, savings have been as high as 50%.
Actual operating temperatures of an electrically-equivalent, aluminum foil strips are from 15 to 20 degrees Fahrenheit cooler than a copper wire wound unit;
Internal hot spots usually encountered in wire windings are substantially eliminated through the use of aluminum foil;
Lower cost insulation materials are generally permissible for foil coils as compared with those demanded by wire, because foil has a substantially lower turn-to-turn voltage drop (difference in potential);
Conductor weight in foil coils is about half of that of equal capacity wound copper wire coils, while the overall size is substantially equivalent to wire coils.
Comments are closed.