Aluminum strip refers to aluminum as the main raw material, and mixed with other alloy elements made of aluminum or aluminum strip. Aluminum strip is an important basic material for the development of China’s national economy. It is widely used in aviation, aerospace, construction, printing, transportation, electronics, chemicals, food, medicine and other industries.
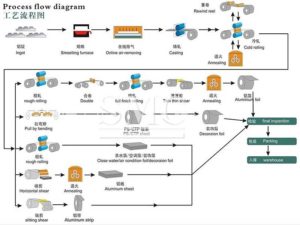
1 casting for aluminum strip
The purpose of the casting is to make the alloy with high purity and meet the requirements of the composition.
Some key parameters in the casting process:
1 furnace temperature is generally set at 1050 C, the process needs to monitor the temperature of the material, control the temperature of the metal does not exceed 770 degrees C
2 at about 735 DEG C, the slag is operated, which is beneficial to the separation of slag and liquid
3 refining is generally the use of the way of the second refining, refining and a solid refining agent, the two refining using gas refining methods.
4 after the furnace is static, the general 30min-1h needs to be cast in time, otherwise it needs to be refined
5 in the casting process, the need to continue to join the Ai-Ti-B wire, in order to refine the grain
2 Hot-rolling for aluminum strip
Hot rolling in general refers to the metal above the recrystallization temperature of the hardening and softening process of metal and hot rolling process, due to the impact of the deformation rate, as long as the recovery and recrystallization process to wait, there will be some hardening. After hot rolling, the recrystallization of the metal is not complete. Hot rolling can improve the processing properties of metals and alloys, reduce or eliminate casting defects.
3 Roll casting for aluminum strip
Casting rolling process: liquid metal, front box (liquid level control), casting mill (lubrication system, cooling water), cutting machine, coiling machine.
Cast rolling temperature is generally between 680 -700 C / C, the lower the better, stable cast rolling line in general more than a month will stop once, the re establishment of the board, the production process needs to strictly control the front box level, to prevent low liquid level. Lubrication of C powder with incomplete combustion of gas, which is one of the reasons that cause the surface of casting roll is dirty. Production speed is generally between 1.5m/min-2.5m/min. The surface quality of casting roll is generally low, which can not meet the requirements of special physical and chemical properties.
4 Cold rolling mills for aluminum strip
Cold rolling refers to the production process of rolling below the recrystallization temperature. During the rolling process, there will be no dynamic recrystallization, and the temperature will rise to the recovery temperature. Cold rolled plate and strip with high dimensional accuracy, good surface quality, uniform structure and performance, with heat treatment can get a variety of state products. Cold rolling can be used to produce thin strip, and it has the disadvantages of large deformation energy consumption and more processing times.
5 Finishing
Finishing is to make the cold rolled sheet to meet the customer requirements of the processing, or in order to facilitate the subsequent processing of products and a processing method. The finishing equipment can be used to correct the defects in hot rolled cold rolling process, such as crack, oil, plate shape, residual stress and so on. Finishing equipment is varied, mainly cross cutting, slitting, stretch bending, annealing furnace, cutting machine, etc..