8011 aluminium strip is one the most popular strips in industrial application. With low hardness, its properties prove to be better than pure aluminium strips. Common tempers for it include O, H18, H19, H14, H22, H24 and H111 etc. Its width ranges from 5mm to 100mm to cater for various application requirements. As for thickness, the most widely acceptable scope is between 0.1mm and 4mm. The strip covers a wide series of application, including materials for aluminum plastic composite pipe, cable wrapping, automobile radiator in water tanks and aluminum tube for kitchen ventilator etc.
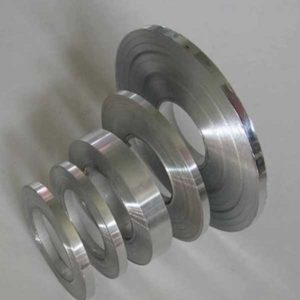
The specification of 8011 aluminium strip varies with different usages. While being used for aluminum plastic composite pipe, it’s generally made into states of O or H22. The thickness is from 0.20mm to 1.5mm and width from 30mm to 250mm. As raw material for cable wrapping, 8011 aluminium strip is usually of O state. In comparison with the previous usage, it becomes much thinner but wider. It’s only between 0.10mm to 0.20mm thick. The smallest width is 100mm, and the biggest 300mm. When applied for automobiles, it has a thickness of 0.08mm to 0.10mm and a wideness of 140mm to 600 mm, the thinnest of all usages. The narrowest of all applications falls on aluminum tube for kitchen ventilators. The strip is only 60mm wide. It’s not thick, either, only 0.10mm to 0.13mm.
All the usages above is based on one extraordinary property of 8011 aluminium strip–corrosion resistance. Aluminum alloys display outstanding anti-rust ability because the element of aluminum reacts to oxygen quickly after being exposed to the air. After the reaction strong and stable oxide aluminum comes into being, acting as a protective layer over the alloys. Therefore, they can be used in severe conditions like ventilators, water tanks and the open air. Besides, the other most existing shape of 8011 alloy is aluminum foil, applied in food and pharmaceutical industries for packaging.
Comments are closed.